Cement Analysis by the Fusion Method per C114
Introduction
Cement is one of the most important materials for construction. Many kinds of hydraulic cements, including Portland cement, with various physical properties are produced by changing the composition of clinker minerals; therefore, it is important to control the chemical composition of cement products and interim products.
Since the fusion method can eliminate sample heterogeneity, such as grain size and mineralogical effects, it is possible to obtain high accuracy for cement samples and also to establish calibrations using a variety of materials. Therefore, X-ray fluorescence (XRF) spectrometry by the fusion method has been the method of choice in cement production processes.
ASTM C114-11 covers chemical analysis of hydraulic cements. In this standard, procedures of wet chemical analysis are mainly described and XRF spectrometry is mentioned as example of “Rapid Test Methods.” In practice, XRF spectrometry has been used for chemical composition analysis of cement owing to its simple sample preparation and high precision.
This application note demonstrates quantitative analysis for Portland and aluminate cements by the fusion method according to ASTM C114-11 on Rigaku Supermini200, a benchtop sequential wavelength dispersive XRF spectrometer.
ASTM C114-11 and calibration standard
The standard ASTM C114-11 has the following descriptions about “Rapid Test Method”:
• Using the test method chosen, make single determinations for each analyte under consideration on at least seven CRM (Certified Reference Material) samples. Complete two rounds of tests on different days repeating all steps of sample preparations. Calculate the differences between values and averages of the values from the two rounds of tests.
• When more than seven CRMs are used in the qualification procedures, at least 77% of the differences between duplicates obtained of any single analytes shall not exceed the limits shown in Table 1 and the remaining differences by no more than twice that value.
• For each analyte and each CRM, the average obtained shall be compared to the certified concentrations. When more than seven CRMs are used in the qualification procedure, at least 77%of the averages for each analytes shall not differ from the certified concentrations by more than the value shown in Table 1, and the remaining average by more than twice that value.
The maximum permissible variations in analysis results defined in ASTM C114-11 are listed in Table 1.
ASTM C114-11 directs that acceptable reference cements are NIST CRMs, or other reference cements traceable to the NIST CRMs.
In this application note, nine NIST CRMs
(SRM1881a, 1882a, 1883a, 1884a, 1885a, 1886a, 1887a, 1888a and 1889a) were used for calibration and a qualification test.
Table 1: Maximum permissible variation
Analyte | Maximum difference between duplicates | Maximum difference of the average of duplicates from the certificate values |
SiO₂ | 0.16 | ±0.2 |
Al₂O₃ | 0.20 | ±0.2 |
Fe₂O₃ | 0.10 | ±0.10 |
CaO | 0.20 | ±0.3 |
MgO | 0.16 | ±0.2 |
SO₃ | 0.03 | ±0.05 |
Na₂O | 0.03 | ±0.05 |
K₂O | 0.02 | ±0.03 |
TiO₂ | 0.03 | ±0.03 |
P₂O₅ | 0.03 | ±0.03 |
ZnO | 0.03 | ±0.03 |
Mn₂O₃ | 0.03 | ±0.03 |
Instrument
The Supermini200, a benchtop sequential wavelength dispersive X-ray fluorescence
(WDXRF) spectrometer, is designed to minimize the peripherals in installation such as cooling water, power supply, installation area, etc. The Supermini200 has good sensitivity for light elements such as Na, Mg and P relative to EDXRF systems, and does not show any spectral overlap between typical analytes for cement, owing to high spectral resolution of the WD optics.
The Supermini200 is equipped with an air-cooled 200 W X-ray tube and up to three analyzing crystals, in which elements from fluorine to uranium can be analyzed. The Supermini200 has the same base software as the ZSX Primus series and, therefore, the software is user-friendly and flexible.
Sample preparation
The samples were ground using a tungsten carbide container with n-hexane (the wet grinding method). Then, the ground fine powder samples were ignited at 950°C for 1 hour. For fusion, 1.0 g of the ignited sample and 4.0 g of flux (lithium tetraborate,
pre-dried at 675°C) were weighed out and mixed. The mixture was fused at 1200°C.
Measurement
Measurements were performed in vacuum on the Supermini200 with a 200 W Pd target X-ray tube for the components listed in Table 1. Measurement condition is shown in Table 2.
Table 2: Measurement condition
X-ray tube | Pd target, 200 W end-window type |
Tube condition | 50 kV and 4.0 mA |
Analysis area | 30 mm in diameter |
Path atmosphere | Vacuum |
Element | Si | Al | Fe | Ca | Mg | Na |
Line | Kα | Kα | Kα | Kα | Kα | Kα |
Primary filter | Out | Out | Out | Out | Out | Out |
Crystal | PET | PET | LiF | PET | RX25 | RX25 |
Detector | PC | PC | SC | PC | PC | PC |
Counting time (s) | 40 | 40 | 20 | 60 | 60 | 60 |
Element | K | Ti | P | Zn | Mn | |
Line | Kα | Kα | Kα | Kα | Kα | |
Primary filter | Al | Out | Out | Out | Out | |
Crystal | PET | LiF | PET | LiF | LiF | |
Detector | PC | SC | PC | SC | SC | |
Counting time (s) | 40 | 20 | 40 | 20 | 20 |
Calibration
The results obtained for the calibration curves are shown in Table 3 and Fig. 1. A matrix correction method is applied to the calibrations.
Figure 1: Calibration curves of Portland and alumina cement.
The symbol ⚬ shows the data point before the correction and the symbol ◆ shows the data after correction in the calibration charts.
The accuracy of calibration is calculated by the following formula:
$Accuracy = \sqrt{ \frac{\sum_i{(C_i-\hat{C}_i)^2}}{n-2} }$
$C_i$: calculated value of standard sample
$\hat{C}_i$: reference value of standard sample
n : number of standard samples.
Table 3: Calibration results (unit: mass%)
Analyte | Calibration range | Accuracy |
SiO₂ | 0.24 - 22.38 | 0.058 |
Al₂O₃ | 3.875 - 70.04 | 0.051 |
Fe₂O₃ | 0.078 - 14.67 | 0.034 |
CaO | 29.52 - 67.87 | 0.086 |
MgO | 0.19 - 4.475 | 0.050 |
SO₃ | 0.021 - 1.068 | 0.024 |
Na₂O | 0.014 - 1.228 | 0.033 |
K₂O | 0.020 - 1.786 | 0.005 |
TiO₂ | 0.003 - 0.306 | 0.004 |
P₂O₅ | 0.001 - 0.107 | 0.001 |
ZnO | 0.003 - 0.259 | 0.006 |
Mn₂O₃ | 0.007 - 0.259 | 0.0029 |
Qualification test for ASTM C114-11
Quantitative analyses have been carried out for the nine NIST SRMs of Portland and alumina cement using the calibration curves obtained above. The results are listed in the Table 4, comparing them with the values of ASTM C114 requirement.The results prove that the analysis method demonstrated in this application note meets the requirements described in ASTM C114-11.
Repeatability test
To demonstrate the stability of the instrument, the duplicated fused beads of NIST SRM 1889a were measured 10 times consecutively. The test results are listed in Table 5. The results show good precision.
In comparison with the values of the limits defined in ASTM C114-11 shown in Table 4, the standard deviations of the repeatability test are sufficiently low. The results demonstrate that the performance of the Supermini200 meets and exceed the precision requirements for analysis of hydraulic cement, including Portland and alumina cements, stated in ASTM C114-11.
Table 4: Qualification test results (unit: mass%)
Analyte | Difference between duplicates | Difference of the average of duplicate from the certificate values | ||
Limit (ASTM) | Maximum difference | Limit (ASTM) | Maximum difference | |
1.4286 in | 0.16 | 0.09 | 0.2 | 0.1 |
Al₂O₃ | 0.20 | 0.09 | 0.2 | 0.2 |
Fe₂O₃ | 0.10 | 0.02 | 0.10 | 0.05 |
CaO | 0.20 | 0.13 | 0.3 | 0.1 |
MgO | 0.16 | 0.05 | 0.2 | 0.1 |
Na₂O | 0.03 | 0.03 | 0.05 | 0.03 |
K₂O | 0.03 | 0.01 | 0.05 | 0.05 |
TiO₂ | 0.02 | 0.01 | 0.03 | 0.01 |
P₂O₅ | 0.03 | 0.003 | 0.03 | 0.01 |
ZnO | 0.03 | 0.001 | 0.03 | 0.002 |
Mn₂O₃ | 0.03 | 0.004 | 0.03 | 0.01 |
Table 5: Repeatability test results (unit: mass%)
Analyte | Certified value (SRM1889a) | Results of 10-time consecutive measurements | |||
1st fused bead | 2nd fused bead | ||||
Average | Standard deviation | Average | Standard deviation | ||
SiO₂ | 20.66 | 20.585 | 0.032 | 20.619 | 0.030 |
Al₂O₃ | 3.89 | 3.805 | 0.032 | 3.806 | 0.019 |
Fe₂O₃ | 1.937 | 1.941 | 0.009 | 1.944 | 0.005 |
CaO | 65.34 | 65.410 | 0.047 | 65.404 | 0.030 |
MgO | 0.814 | 0.747 | 0.012 | 0.751 | 0.012 |
Na₂O | 0.195 | 0.200 | 0.017 | 0.193 | 0.019 |
K₂O | 0.605 | 0.622 | 0.007 | 0.623 | 0.010 |
TiO₂ | 0.227 | 0.231 | 0.007 | 0.231 | 0.007 |
P₂O5 | 0.110 | 0.114 | 0.002 | 0.114 | 0.002 |
ZnO | 0.0048 | 0.0044 | 0.0008 | 0.0047 | 0.0007 |
Mn₂O₃ | 0.2588 | 0.2565 | 0.0033 | 0.2573 | 0.0027 |
Conclusion
The qualification test for ASTM C114-11 demonstrated that the test results on the Supermini200 by the fusion method meet and/or exceed the requirements for analysis of hydraulic cement defined in ASTM C114-11.
Application Note XRF1046 reported that the qualification test results for ASTM C114-11 on the Supermini200 by the pressed powder method meet the requirements, using only Portland cement. Since the fusion method is employed in the analysis demonstrated in this application note, it is possible to establish a single calibration for wide concentration ranges, including both Portland and alumina cements. The precision obtained by the repeatability test is much better than the defined values required in ASTM C114-11.
The Supermini200 is a wavelength dispersive benchtop X-ray fluorescence spectrometer equipped with a newly developed high-power
air-cooled X-ray tube that does not require cooling water. The spectrometer configuration results in high sensitivity, relative to benchtop energy dispersive XRF spectrometers, for light elements such as Na or Mg, as well as heavy elements.
References
[1] ASTM C114-11 Standard Test Methods for Chemical Analysis of Hydraulic Cement
[2] Application Note XRF1046 Cement Analysis by the Pressed Powder Method on Benchtop WDXRF Supermini200 According to ASTM C114-11
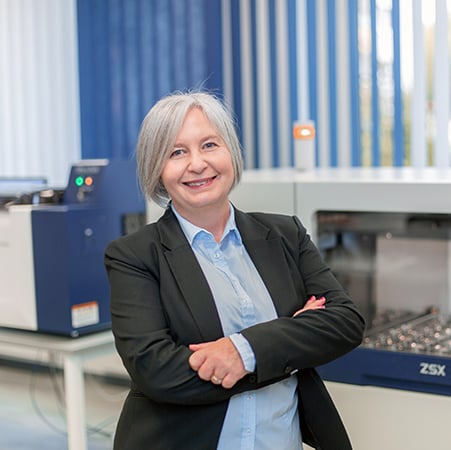
Contact Us
Whether you're interested in getting a quote, want a demo, need technical support, or simply have a question, we're here to help.