Fused Bead Analysis for Wide Concentration Ranges of Various Oxide Materials on Benchtop WDXRF
Introduction
The fusion method in X-ray fluorescence (XRF) analysis is an effective sample preparation technique for getting accurate analysis results of powder samples, since the technique eliminates heterogeneity due to grain size and mineralogical difference. In addition, the homogenization of material property by vitrification makes it possible to expand the calibration range by the use of synthetic standards of fused beads with reagents or by using diverse reference materials. This application note demonstrates that single calibration for diverse materials, such as minerals, ores and refractories, was established by the fusion method on the Supermini200, a benchtop wavelength dispersive (WD) XRF spectrometer.
Instrument
The Supermini200, a benchtop sequential WDXRF spectrometer, is designed to minimize the peripherals in installation such as cooling water, power supply, installation area, etc. The Supermini200 has good sensitivity for the light elements such as Na, Mg and P, relative to energy dispersive (ED) XRF systems, and does not show any spectral overlap between typical analytes for cement, owing to high spectral resolution of the WD optics.
The Supermini200, equipped with an air-cooled 200 W X-ray tube and up to three analyzing crystals, can analyze the elements from oxygen to uranium.
Fusion bead correction
In XRF analysis by the fusion method for minerals, ores and refractories, it is necessary to apply different fusion conditions, such as dilution ratio, oxidizing agent, due to the difference of the optimum conditions for each material. In addition, some samples have crystal water or carbonate, which result in loss on ignition (LOI); on the other hand, some samples show gain on ignition (GOI).
“Fusion Bead Correction”, an optional program of the ZSX software, mounted on the Supermini200, can apply correction for error factors in the fusion method, such as difference of the mixing ratio of flux and oxidizing agent to sample, LOI and/or GOI, as well as matrix correction for absorption and enhancement by co-existing elements. The Fusion Bead Correction plays an important role in the analysis demonstrated in this application note.
Table 1: Standard materials used
BAS
Number | Material |
BAS203a | Talc |
BCS313-1 | High purity silica |
BCS314 | Silica brick |
BCS315 | Fire brick |
BCS368 | Dolomite |
BCS369 | Magnesite chrome (Chrome-magnesia) |
BCS370 | Magnesite chrome (Chrome-magnesia) |
BCS375 | Soda feldspar |
BCS376 | Potash feldspar |
BCS358 | Zirconia |
BCS389 | High purity magnesia |
BCS393 | Limestone |
BCS394 | Calcined Bauxite |
BCS395 | Bauxite |
BAS 683 | Iron Ore |
NIST
Number | Material |
NBS98a | Plastic Clay |
NBS120c | Florida Phosphate Rock |
SRM 1c | Argillaceous Limestone |
SRM 69b | Bauxite (Arkansas) |
SRM 696 | Bauxite, Surinam |
SRM 697 | Bauxite, Dominican |
SRM 698 | Bauxite, Jamaican |
SRM 70a | Feldspar, Potash |
SRM 99a | Feldspar, Soda |
NIST81a | Glass Sand |
NIST1413 | Glass Sand (High Alumina) |
NBS694 | Phosphate Rock, Western |
CSJ
Number | Material |
R-603 | Clay |
R-701 | Feldspar |
R-801 | Agalmatolite |
TARJ
TARJ | |
Number | Material |
JRRM511 | Chrom-magnesia refractory |
JRRM602 | Zircon-zirconia refractory |
JRRM701 | Alumina-zircon-silica refractory |
JCA
Number | Material |
RM-611 | Portland cement |
RM-612 | Portland cement |
RM-613 | Portland cement |
ECISS
Number | Material |
ECISS782 | Dolomite |
ECISS776 | Fire Brick |
JSS
Number | Material |
JSS009-2 | Pure iron oxide (III) |
Standard samples
Table 1 lists the certified reference materials used in this experiment. To expand the calibration range, reagents were used to make synthetic fused beads for some components, which is summarized in Table 2. Table 3 shows the concentration range of for only the reference materials and the calibration range including the synthetic fused beads for each component.
Sample preparation
Lithium tetraborate (Li₂B₄O₇), the flux used in this analysis, was dried at 675°C. The dilution (mixing) ratio of sample to flux in weight was 1:10 for all the materials except 1:20 for chrome-magnesia refractory. Lithium nitrate, an oxidizing agent, was used only for chrome-magnesia refractory, where the weight ratio of sample to flux was 1:10.
The samples were fused on Rigaku benchtop high-frequency fusion machine. The fusion temperature was 1200°C for all the materials except for Portland cement, which was fused at 1075°C to prevent volatilization of sulfur.
Measurement condition
Each fused bead was measured under vacuum on the Supermini200, a benchtop WDXRF spectrometer, which was equipped with an end-window Pd-target 200 W X-ray tube, operating at 50 kV and 4.0 mA, with the measurement area 30 mm in diameter. The measurement condition of each component was tabulated in Table 4. The counting time for each element is 20 seconds each for peak and background. The total measurement time for the analysis of the 15 components per sample was approximately 12 minutes.
Table 2: Synthetic fused bead (unit: mass%)
Reagent | Component | Content of component | Content of LOI |
Na₂CO₃ | Na₂O | 25 | 75 |
Al₂O₃ | Al₂O₃ | 100 | 0 |
Li₃PO₄ | P₂O₅ | 25 | 75 |
K₂CO₃ | K₂O | 50 | 50 |
CaCO₃ | CaO | 100 | 0 |
TiO₂ | TiO₂ | 10 | 90 |
Table 3: Concentration range of the reference materials and the calibration (unit: mass%)
Component | Concentration range of the reference materials | Calibration range |
Na₂O | 0.003 - 10.4 | 0.003 - 25.0 |
MgO | 0.001 - 96.7 | 0.001 - 96.7 |
Al₂O₃ | 0.036 - 88.8 | 0.036 - 100 |
SiO₂ | 0.2 - 99.78 | 0.2 - 99.78 |
P₂O₅ | 0.004 - 33.34 | 0.004 - 33.34 |
K₂O | 0.004 - 11.8 | 0.004 - 50.0 |
CaO | 0.006 - 66.25 | 0.006 - 100 |
TiO₂ | 0.004 - 4.961 | 0.004 - 10.0 |
MnO | 0.000 - 0.596 | 0.000 - 0.596 |
Fe₂O₃ | 0.012 - 99.84 | 0.012 - 99.84 |
Cr₂O₃ | 0.001 - 52.51 | 0.001 - 52.51 |
ZrO₂ | 0.034 - 92.7 | 0.034 - 92.7 |
HfO₂ | 0.00 - 1.63 | 0.00 - 1.63 |
SO₃ | 0.001 - 6.07 | 0.001 - 6.07 |
SrO | 0.003 - 0.28 | 0.003 - 0.28 |
LOI | 0.00 - 47.4 | 0.00 - 90.0 |
Note) Underlined numbers denote the concentration of the synthetic fused bead.
Table 4: Measurement condition
Element | Na | Mg | Al | Si | P | S | K | Ca |
Line | Kα | Kα | Kα | Kα | Kα | Kα | Kα | Kα |
Filter | Out | Out | Out | Out | Out | Out | Al | Out |
Crystal | RX25 | RX25 | PET | PET | PET | PET | PET | PET |
Detector | PC | PC | PC | PC | PC | PC | PC | PC |
Element | Ti | Cr | Mn | Fe | Sr | Zr | Hf | |
Line | Kα | Kα | Kα | Kα | Kα | Lα | Lβ1 | |
Filter | Out | Out | Out | Out | Out | Out | Out | |
Crystal | LiF | LiF | LiF | LiF | LiF | PET | LiF | |
Detector | SC | SC | SC | SC | SC | PC | SC |
Calibration result
The calibration results are summarized in Table 5 and typical calibration curves are shown in Figures 1 – 8, where some typical materials are displayed on the charts in order to indicate that various materials were used for the calibration.
The accuracy of calibration is calculated by the following formula:
$Accuracy = \sqrt{ \frac{\sum_i{(C_i-\hat{C}_i)^2}}{n-m} }$
$C_i$: calculated value of standard sample
$\hat{C}_i$: reference value of standard sample
n : number of standard samples.
m: degree of freedom (linear 2, quad. 3)
When matrix correction coefficients were calculated theoretically, LOI/GOI was designated as the balance component in the de Jongh model, where an analyte is included in the correcting components, to compensate for the influence of LOI/GOI. Therefore, it is not necessary to obtain LOI/GOI content or to ignite samples prior to the analysis of unknown samples though the LOI/GOI content is unknown.
The calibration results show that excellent accuracy was obtained for each and all of the analytes even though various standard materials and additional synthetic standards were used for making the calibration curves.
When an element line of an analyte is interfered with by other element lines, it is necessary to apply appropriate overlap correction. In this analysis, correction for overlap of Zr-Lα to P-Kα, of Cr-Kβ1 to Mn-Kα, of P-Kα to Zr-Lα and of Zr-Lγ1 to S-Kα was carried out.
Table 5: Calibration summary
Component | Calibration range (mass%) | Accuracy (mass%) | Figure |
SiO₂ | 0.2 - 99.78 | 0.27 | 1 |
Al₂O₃ | 0.036 - 100 | 0.26 | 2 |
MgO | 0.001 - 96.7 | 0.18 | 3 |
Na₂O | 0.003 - 25.0 | 0.075 | 4 |
CaO | 0.006 - 100 | 0.30 | 5 |
K₂O | 0.004 - 50.0 | 0.032 | |
P₂O₅ | 0.004 - 33.34 | 0.049 | |
TiO₂ | 0.004 - 10.0 | 0.043 | |
MnO | 0.000 - 0.596 | 0.067 | |
Fe₂O₃ | 0.012 - 99.84 | 0.26 | 6 |
Cr₂O₃ | 0.001 - 52.51 | 0.038 | |
ZrO₂ | 0.034 - 92.7 | 0.34 | 7 |
HfO₂ | 0.00 - 1.63 | 0.035 | |
SO₃ | 0.001 - 6.07 | 0.031 | 8 |
SrO | 0.003 - 0.28 | 0.003 |
Figure 1: SiO₂ calibration curve
Figure 2: Al₂O₃ calibration curve
Figure 3: MgO calibration curve
Figure 4: Na₂O calibration curve
Figure 5: CaO calibration curve
Figure 6: Fe₂O₃ calibration curve
Figure 7: ZrO₂ calibration curve
Figure 8: SO₃ calibration curve
Conclusion
This application note demonstrated that the fusion method and the corrections for LOI/GOI and dilution ratio of flux and oxidizing agent enable a single calibration with the wide range of concentration and for diverse materials, such as natural minerals and ores. In addition, the note also showed that it was possible to extend the calibration range by the use of a single agent to make a synthetic standard fused bead.
The Supermini200 is a benchtop WDXRF spectrometer equipped with an air-cooled 200 W X-ray tube to deliver excellent sensitivity and resolution from light elements to heavy elements while eliminating typical installation requirements, such as cooling water, special power supply and large floor space. Therefore, this system can be used for analysis of wide variety of natural minerals and ores under various environments.
References
(1) Y. Yamada: Rigaku Journal, 28[2] (2012), 15–21.
(2) Rigaku Application Note XRF5027, Determination of Metals in Copper Concentrate by Advanced Correction Method for Fused Beads
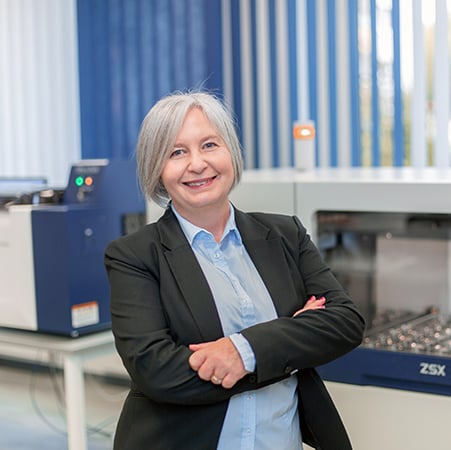
Contact Us
Whether you're interested in getting a quote, want a demo, need technical support, or simply have a question, we're here to help.